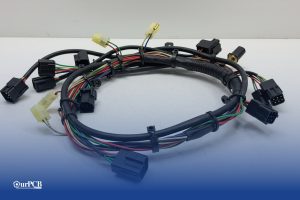
Best 15 Automotive Wire Harness Manufacturers 2025
Would your car be able to run without wire harnesses? Not a chance. Wire harnesses connect all the electrical parts together. No harness means no
OurPCB is a leading LED PCB manufacturer, specializing in custom PCB design, fabrication, and assembly for lighting, automotive, and industrial applications. We ensure superior heat management, durability, and energy efficiency, delivering high-quality LED circuit boards with precision and reliability.
At OurPCB, we specialize in custom LED PCBs, tailoring every aspect to meet specific client needs. We offer a range of materials, including FR-4, aluminum, and flexible substrates, carefully selected for their thermal conductivity, durability, and suitability for each application. To enhance LED performance and longevity, we incorporate optimized thermal management features that ensure efficient heat dissipation.
If you have a unique product idea, our experienced engineers provide custom design support, working closely with you to develop prototypes that align with your specifications. Through our rapid prototyping and rigorous testing, we validate designs before mass production, ensuring they meet industry standards and deliver reliable performance.
LED technology has transformed the way we illuminate our environments, offering energy-efficient and long-lasting solutions. OurPCB understands that different applications require specific design considerations, and we are equipped to deliver custom LED circuit boards for a variety of uses:
As a manufacturer of LED PCBs, we design and produce a variety of circuit boards tailored for different applications and performance requirements. Each type serves a unique purpose, ensuring optimal efficiency, durability, and thermal management for LED-based products.
Rigid LED PCBs are built from FR-4 material, providing strong structural support for applications where bending is not required. These are commonly used in lighting fixtures, automotive lighting, and electronic devices, offering high-density component placement and reliable performance.
Flexible LED PCBs utilize bendable materials, making them ideal for wearable devices, LED strips, and curved lighting where space constraints demand adaptability. Their design versatility allows seamless integration into compact or irregularly shaped products.
Rigid-Flex LED PCBs combine both rigid and flexible layers, making them suitable for medical devices, aerospace applications, and high-end consumer electronics. By reducing interconnects, they save space and improve reliability, especially in dynamic environments.
Aluminum LED PCBs feature an aluminum base layer, enhancing heat dissipation for high-power LED applications such as automotive headlights, industrial lighting, and high-intensity illumination systems. This material extends the lifespan and efficiency of LEDs by preventing overheating.
Copper LED PCBs offer even higher thermal conductivity than aluminum, making them ideal for high-performance, high-power LED applications that demand superior heat management. These are commonly used in advanced industrial and high-output lighting systems.
High-Frequency LED PCBs are designed for communication devices and high-speed electronics where minimizing signal loss is critical. These boards ensure signal integrity and reduce electromagnetic interference, making them suitable for high-precision LED applications.
Multilayer LED PCBs consist of multiple conductive layers, enabling complex circuit designs in smart lighting systems and advanced electronic devices. By allowing more components in a compact space, they enhance functionality without increasing size.
We handle everything from parts sourcing to final assembly, providing a hassle-free experience that ensures top-quality boards every time.
Whether you need a few prototypes or large-volume batches, our flexible assembly services adapt to your project’s scope and timeline.
Stay environmentally responsible with our compliant assembly processes, offering RoHS and lead-free options for safe, reliable builds.
No matter the complexity, we can assemble boards of all configurations—single-layer, multi-layer, or a mix—to match your exact specifications.
From one-off prototypes to bulk orders, we accommodate projects of all sizes without compromising on quality or turnaround time.
Join our growing community of satisfied clients who rely on our dependable assembly expertise and dedicated customer support.
Mon-Fri: 24 hours,
Sat: 9am-6pm, GMT+8
Reach us at
[email protected]
24 hours online
+86-199-30589219
Mon-Fri: 24 hours,
Sat: 9am-6pm, GMT+8
An LED PCB is a printed circuit board designed to mount and power light-emitting diodes (LEDs). It requires effective heat dissipation due to high temperatures generated during operation. Aluminum-based (metal core) PCBs are commonly used for better thermal management. Most LED devices use SMD packaging, connecting multiple LEDs for optimal lighting.
An LED PCB offers multiple benefits, including a longer lifespan of up to 25,000 hours, high efficiency with minimal energy loss, and a compact design ideal for various applications. It is also environmentally friendly, free of harmful substances, and reduces power consumption by up to 90%, lowering costs.
LED PCB design faces challenges like heat management, requiring aluminum substrates or heat sinks to prevent overheating. Material selection is crucial for efficient heat dissipation. Current control ensures LEDs receive the right power, avoiding damage. Trace routing and component placement must be optimized to prevent short circuits and performance issues.
An LED PCB board consists of four main layers: a metal substrate (usually aluminum) for heat dissipation, an insulation layer for electrical separation, copper traces for conductivity, and a solder mask to prevent short circuits and corrosion. Additionally. a silkscreen adds markings, while LED chips emit light when powered.
Would your car be able to run without wire harnesses? Not a chance. Wire harnesses connect all the electrical parts together. No harness means no
Making wire harnesses isn’t complicated. At OurPCB, we create custom wire harnesses for an expansive range of industries every day. While it’s a complicated process,
Prototype cable assemblies are the very important place in between PCB design ideas and interconnects. OurPCB brings prototype assemblies with PCB solutions to your tables.
PCB thermal management prevents component overheating through strategic heat transfer techniques. Without proper thermal control, electronics are at risk of electronic failures through weakened solder
ContentsKey TakeawaysWhat is a Multilayer-Printed Circuit Board?How do Multilayer PCB Boards Work?Multilayer PCB ApplicationsMultilayer PCB Manufacturing Process: StepsMultilayer PCB Manufacturing MachinesBenefits of Multilayer Circuit BoardsWhat
As electronics continue to miniaturize while processing power increases, the resulting thermal challenges make high-Tg PCBs increasingly essential for modern electronic design. ContentsKey TakeawaysWhat is
We use cookies to improve your browsing experience, which may include personal information. By clicking "Agree," you accept our Privacy Policy and cookie use. You can change your cookie settings in your browser anytime.
Agree