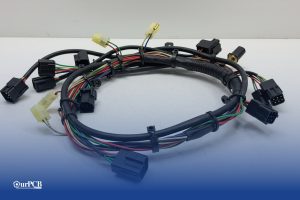
Best 15 Automotive Wire Harness Manufacturers 2025
Would your car be able to run without wire harnesses? Not a chance. Wire harnesses connect all the electrical parts together. No harness means no
OurPCB provides PCB manufacturing and prototyping services with a focus on controlled impedance to support high-speed signal performance. Controlled impedance ensures signal integrity in high-speed PCB designs by maintaining consistent impedance throughout traces. We design printed circuit boards with impedance requirements tailored for reliable performance in RF, high-speed digital, and mixed-signal applications.
As electronic devices advance, they use more powerful components and drivers that communicate through high-power, high-frequency signals. Traditional copper signal trace designs are not capable of handling this performance. However, you can design a controlled impedance PCB to take care of this.
With PCB-controlled impedance, you get several improvements, such as thicker and wider copper traces to transmit high-speed signals. At OurPCB, our manufacturing process places a focus on controlled impedance designs to ensure optimal performance for high-speed applications. If you’re interested in our services, feel free to request a PCB assembly quote to learn more!
Impedance is a measure of the total opposition that a circuit presents to alternating current (AC) when a voltage is applied. An impedance value is usually represented by the symbol Z and is measured in ohms (Ω). Moreover, impedance is an important concept in electrical engineering and electronics.
Specific impedance values can vary depending on the application and the specific requirements of a circuit. Here are a few common impedance values used in electronics and PCB impedance design:
Standard impedance value used in many high-frequency applications, including radio frequency (RF) circuits and test equipment
Used in video and cable television applications
Often used in differential impedance signaling applications, such as Ethernet and USB
Used in some antenna systems and older television applications
Let’s get into why PCB impedance control is important. Essentially, it plays a major role in high-speed and high-frequency PCB designs. It improves the performance and reliability of electronic devices. Here are a few other reasons why impedance control is influential in PCBs.
With controlled signal integrity, you will have clean and reliable PCB signal traces and transmissions. A controlled impedance trace can minimize signal reflections and distortions and can maintain quality over a long PCB trace.
With a trace impedance mismatch, you may be faced with increased rise and fall times, ringing and overshoot, false logic circuit triggers, and more.
Impedance control can help manage power distribution and reduce noise in power delivery systems. Essentially, maximum power is transferred only when the source impedance matches the load impedance.
In PCB assembly and design, a controlled PCB transmission line will ensure efficient power delivery to components and optimize signal strength in communication systems.
When you specify impedance control in PCBs, you can minimize electromagnetic interference (EMI) and improve the overall performance of your system. Impedance control is also important for meeting regulatory requirements, reducing interference with other devices, and improving overall system reliability, all of which contribute to maintaining optimal signal integrity.
A PCB manufacturer will ensure impedance control because it’s essential for high-speed digital circuits. It is also incredibly important for RF and microwave applications.
With controlled signal integrity, you will have clean and reliable PCB signal traces and transmissions. A controlled impedance trace can minimize signal reflections and distortions and can maintain quality over a long PCB trace.
With a trace impedance mismatch, you may be faced with increased rise and fall times, ringing and overshoot, false logic circuit triggers, and more.
Impedance control can help manage power distribution and reduce noise in power delivery systems. Essentially, maximum power is transferred only when the source impedance matches the load impedance.
In PCB assembly and design, a controlled PCB transmission line will ensure efficient power delivery to components and optimize signal strength in communication systems.
When you specify impedance control in PCBs, you can minimize electromagnetic interference (EMI) and improve the overall performance of your system. Impedance control is also important for meeting regulatory requirements, reducing interference with other devices, and improving overall system reliability, all of which contribute to maintaining optimal signal integrity.
A PCB manufacturer will ensure impedance control because it’s essential for high-speed digital circuits. It is also incredibly important for RF and microwave applications.
Achieving uniform controlled impedance in a PCB involves careful planning, design, and manufacturing considerations. Here’s a step-by-step guide to help you understand how to achieve controlled impedance at each point.
The first step is to define your impedance target. For single-ended traces on the PCB, the most common values are 50 Ω, 75 Ω, and 100 Ω. Differential pairs are 90 Ω, 100 Ω, and 120 Ω. Then, you’re going to have to determine the frequency range of operation, as this affects the material selection and design rules.
Finally, specify your impedance tolerance limits. This is usually about 10%, but it can be tighter for more critical applications.
It’s important to choose the right PCB stackup. Select FR-4 for lower frequencies, but select high-frequency laminates for RF applications.
Lower dielectric constant (Dk) materials typically offer improved performance, while lower dissipation factor (Df) reduces signal loss. Then, be sure to choose the correct copper weight, often between 0.5 to 2 oz per square foot
Start by figuring out how many layers you’ll need; more layers provide you with better control, but they also increase the cost.
Arrange the signal and plane layers, typically as signal-ground-power-signal. Then, you’ll calculate the dielectric thickness using impedance calculators or specialized software. For more complex designs, you might want to use buried and blind vias.
Use impedance calculation formulas or software to calculate trace dimensions. You’ll need to determine trace width and spacing and adjust these to calculate the impedance value. Also, keep in mind manufacturing tolerances. If you have differential pairs, you’ll have to calculate the individual trace width and the spacing between traces.
Set up the trace width and spacing rules in your CAD software and define size, spacing, and type via routes. Then you need to establish clearance rules for between traces, pads, and planes. Create length-matching rules for differential pairs.
Place components to minimize critical trace lengths. Route critical signals first with consistent width and smooth bends. Use reference planes for return paths and route differential pairs as parallel, equal-length traces with length matching. Finally, add guard traces and stitching vias to control crosstalk.
Start by performing a pre-layout simulation using tools like HyperLynx or HFSS. Then, conduct a post-layout simulation to verify impedance control and make sure to check for reflections, crosstalk, and EMI issues.
Analyze eye diagrams to ensure that signal quality meets specifications and iterate design if necessary by adjusting trace widths, spacings, or stackup.
Generate accurate Gerber files and include impedance requirements in fabrication notes. Specify impedance control requirements, including target impedances for different trace types and acceptable tolerance ranges.
Then, request impedance coupons and test structures for impedance verification. Finally, choose a PCB manufacturer experienced in characteristic impedance control, like OurPCB.
Perform Time Domain Reflectometry (TDR) measurements to verify actual trace impedance. Use Vector Network Analyzer (VNA) for high-frequency testing to measure S-parameters. Then, conduct functional testing to ensure the PCB meets performance requirements. Analyze test results and make adjustments if necessary.
We handle everything from parts sourcing to final assembly, providing a hassle-free experience that ensures top-quality boards every time.
Whether you need a few prototypes or large-volume batches, our flexible assembly services adapt to your project’s scope and timeline.
Stay environmentally responsible with our compliant assembly processes, offering RoHS and lead-free options for safe, reliable builds.
No matter the complexity, we can assemble boards of all configurations—single-layer, multi-layer, or a mix—to match your exact specifications.
From one-off prototypes to bulk orders, we accommodate projects of all sizes without compromising on quality or turnaround time.
Join our growing community of satisfied clients who rely on our dependable assembly expertise and dedicated customer support.
Mon-Fri: 24 hours,
Sat: 9am-6pm, GMT+8
Reach us at
[email protected]
24 hours online
+86-199-30589219
Mon-Fri: 24 hours,
Sat: 9am-6pm, GMT+8
Without controlled impedance, you can experience unreliable operation, increased bit error rates, and in some cases, complete system failure. Particularly, you might see signal reflections, reduced signal integrity, EMI problems, power loss, and reduced maximum operating frequency.
The dielectric constant affects the speed at which signals travel through the PCB. A lower Dk results in faster signal propagation and wider traces. The dielectric constant is an important part of calculating the impedance of a transmission line.
Controlled impedance is essential for ensuring signal integrity in a variety of PCB applications, including:
Controlled impedance is also critical in telecommunications and high-speed computing to prevent signal distortion, reflections, and crosstalk.
Would your car be able to run without wire harnesses? Not a chance. Wire harnesses connect all the electrical parts together. No harness means no
Making wire harnesses isn’t complicated. At OurPCB, we create custom wire harnesses for an expansive range of industries every day. While it’s a complicated process,
Prototype cable assemblies are the very important place in between PCB design ideas and interconnects. OurPCB brings prototype assemblies with PCB solutions to your tables.
PCB thermal management prevents component overheating through strategic heat transfer techniques. Without proper thermal control, electronics are at risk of electronic failures through weakened solder
ContentsKey TakeawaysWhat is a Multilayer-Printed Circuit Board?How do Multilayer PCB Boards Work?Multilayer PCB ApplicationsMultilayer PCB Manufacturing Process: StepsMultilayer PCB Manufacturing MachinesBenefits of Multilayer Circuit BoardsWhat
As electronics continue to miniaturize while processing power increases, the resulting thermal challenges make high-Tg PCBs increasingly essential for modern electronic design. ContentsKey TakeawaysWhat is
We use cookies to improve your browsing experience, which may include personal information. By clicking "Agree," you accept our Privacy Policy and cookie use. You can change your cookie settings in your browser anytime.
Agree