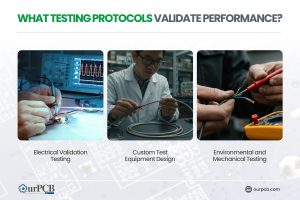
Prototype Cable Assemblies
Prototype cable assemblies are the very important place in between PCB design ideas and interconnects. OurPCB brings prototype assemblies with PCB solutions to your tables.
Looking for a reliable copper core PCB manufacturer for your high-performance electronic applications? OurPCB delivers exceptional metal core PCB solutions with superior thermal conductivity for demanding projects. As a leading copper base PCB supplier in China, we specialize in advanced PCB fabrication techniques that ensure optimal heat dissipation for your most challenging designs.
Copper core PCBs are specialized metal-based PCB board designs that use copper as the substrate material for exceptional thermal management. These advanced circuit boards feature a layered construction with a copper base, dielectric layer, and circuit layer that delivers thermal conductivity of 380-400 W/mK—dramatically outperforming standard FR4 PCB materials. High-power applications like LED lighting, automotive systems, and power controllers require this superior heat dispersion to prevent component failure.
Our copper substrate PCBs provide the ideal solution when standard printed circuit board options can’t handle your thermal requirements. As both a copper core PCB factory and MCPCB manufacturer, OurPCB delivers custom copper solutions that maintain reliability in extreme operating conditions.
Copper core PCBs provide exceptional thermal management that extends component lifespan and improves overall device reliability. Your high-power applications benefit from the advantage of copper’s natural ability to dissipate heat, nearly times better than aluminum PCBs, while maintaining electrical isolation for sensitive components.
This comprehensive PCB assembly with components process ensures consistent quality, minimizes defects, and delivers fully functional electronic products that meet your specifications and timeline requirements. From solder paste application to wave soldering, every step receives meticulous attention.
OurPCB delivers industry-leading copper-based PCB design and fabrication with advanced capabilities that exceed industry standards. Our specialized equipment and engineering expertise ensure your core printed circuit projects achieve optimal performance while meeting strict reliability requirements.
Copper core PCBs differ from standard circuit boards through their specialized multi-layer structure designed for superior thermal performance. The foundation of every metal core printed circuit board is a solid copper plate that efficiently conducts heat away from critical board components. This metal substrate is covered with a high-performance insulated metal layer that provides electrical isolation while still allowing heat transfer. Copper PCBs are then topped with copper foil where components are mounted.
PCB Type | Thermal Conductivity | Max Operating Temperature | Typical Applications |
---|---|---|---|
Copper Core PCB | 380-400 W/mK | Up to 150 °C | High-power LED, Automotive, Power supplies |
Aluminum PCB | 150-220 W/mK | Up to 130 °C | Medium-power LED, Motor drives |
FR4 PCB | 0.3-0.5 W/mK | Up to 130 °C | General electronics, Signal processing |
PCB Type | Thermal Conductivity | Max Operating Temperature | Typical Applications |
---|---|---|---|
Copper Core PCB | 380-400 W/mK | Up to 150 °C | High-power LED, Automotive, Power supplies |
Aluminum PCB | 150-220 W/mK | Up to 130 °C | Medium-power LED, Motor drives |
FR4 PCB | 0.3-0.5 W/mK | Up to 130 °C | General electronics, Signal processing |
OurPCB has developed several cutting-edge copper core circuit structures that deliver exceptional performance for specialized applications. Our research team has pioneered these advanced PCB circuit designs based on proven thermal management principles.
Our LED copper core PCB suppliers serve diverse industries requiring reliable operation under high-power conditions. While the expensive metal core PCB approach costs more than standard options, the performance benefits justify the investment for critical applications.
OurPCB provides a wide array of PCB assembly solutions designed to meet various project requirements. We deliver a combination of accuracy, efficiency, and rigorous quality assurance at every step.
We are proficient in Surface Mount Technology (SMT) assembly, perfect for compact and high-performance electronic products. Utilizing state-of-the-art pick-and-place machines, we ensure precise placement of components.
We offer versatile assembly options to suit your preferences. You can supply your own components, or choose our turnkey service, which includes sourcing, assembly, and delivery of the finished boards.
Our custom assembly service is tailored to your specific designs and special needs. We manage complex layouts and work closely with you to ensure all your requirements are fully met.
We specialize in rapid and reliable PCB assembly. Our quick turn service provides high-quality boards within tight deadlines, all while maintaining strict quality standards.
We produce PCBs that meet IPC Class 3 certification, which is critical for industries such as aerospace and medical. These assemblies guarantee the highest level of reliability for mission-critical applications.
We handle the assembly of all types of IC packages with high precision, including BGAs, POPs, CGAs, QFNs, DFNs, and CSPs. Our advanced machinery allows us to efficiently manage even the most complex IC packages.
As an experienced core PCB manufacturer, OurPCB provides comprehensive copper core PCB fabrication capabilities for diverse technical requirements. Our advanced facility can produce 1 to 8-layer copper core PCB designs with copper thickness options ranging from 35μm to thicker copper foil at 350μm for extreme copper PCB applications.
Technical Parameter | OurPCB Capabilities | Application Benefit |
---|---|---|
Layer count | Multilayer metal core PCB manufacturer (1-8 layers) | Supports complex circuit designs |
Board dimensions | Single-sided PCB to large format | Accommodates varied application needs |
Copper thickness | Heavy copper PCB options from 35μm to 350μm | Customizable power handling capacity |
Min trace width/space | 0.1 mm/0.1 mm | Enables high-density designs |
Structure types | Clad PCB and advanced variants | Maximizes design flexibility |
Our manufacturing process incorporates precision-controlled lamination at 180-220 °C with 200-400 psi pressure for optimal bonding between the PCB substrate and dielectric materials. The copper used in our process undergoes rigorous surface preparation with micro-etching to achieve bond strength exceeding 1.0 N/mm. Whether you select PCB or copper as your primary consideration, our manufacturing system delivers consistent quality.
Our circuit board offers exceptional thermal performance through our proprietary polymer dielectric formulation with 12-18 W/m·K thermal conductivity—a critical parameter for selecting the right PCB for your project. The core PCB uses specially formulated dielectric material composed of ceramic fillers in epoxy resin matrix with dielectric constant (Dk) values of 4.2-4.8.
Beyond standard copper base PCBs, we offer several specialized structure options:
Structure Type | Description | Ideal Applications |
---|---|---|
Direct Thermal Path | Need copper core with minimal insulation | 1000W+ LED lighting, Power converters |
COB Copper PCB | Direct chip-on-board mounting | LED copper core PCB applications |
Hybrid Lamination | Metal base with specialized layers | Mixed-signal circuits, RF power amplifiers |
Embedded Copper | Core PCBs were initially created for power supplies | High-density power distribution |
Ready to enhance your high-power electronic designs with superior thermal management and metal core PCBs, including aluminum or copper? Contact our copper PCB factories today for a detailed consultation and manufacturing quote tailored to your specific PCB needs. Our engineering team will help you determine if you need copper or another solution for your project.
As a contract manufacturer specializing in electronic manufacturing, we’ve invested in advanced assembly equipment that enables us to work with components such as resistors, capacitors, and integrated circuits with exceptional precision. Our PCB assembly rotation component factories utilize both automated processes and skilled manual techniques when assembling components on boards.
Our pick-and-place process achieves industry-leading component placement accuracy of ±0.015 mm, significantly exceeding IPC-9850 requirements. For ultra-miniature applications, we employ vacuum-assisted pick heads with optical centering verification to ensure precise alignment of 01005 and 008004 package sizes.
Technology | Applications | Advantages | Capabilities |
---|---|---|---|
Surface Mount Technology (SMT) | High-density designs, Consumer electronics, Telecommunications equipment | Higher component density, Smaller finished PCB, Automated assembly | Surface mount components down to 01005 size, Fine-pitch BGAs, QFN packages |
Through-Hole Technology (THT) | Industrial equipment, Power systems, High-reliability applications | Superior mechanical strength, Better performance in harsh environments | Through-hole components like connectors, transformers, large capacitors, DIP ICs |
Selective Soldering | Mixed technology boards, High-reliability applications | Precise solder control, Reduced thermal stress | Programmed multipoint soldering, Component-specific parameters |
Mixed Assembly | Complex electronic systems, Medical devices, Automotive electronics | Combines benefits of both SMT and THT, Optimal design flexibility | Simultaneous SMT/THT on single PCB, Complex component integration |
Our flexible technology enables our PCB components assembly factory to accommodate virtually any requirement, from simple single-sided boards to complex multilayer designs with both SMD components and plated through-hole components.
Quality is built into every stage of our PCB component assembly machine operations. We adhere to rigorous international standards to ensure consistent, reliable results in our PCB manufacturing process:
Standard | Description | Implementation at OurPCB |
---|---|---|
IPC-A-610 | Acceptability of Electronic Assemblies | Class 2 (standard) and Class 3 (high-reliability) options available |
IPC-J-STD-001 | Requirements for Soldered Electrical and Electronic Assemblies | Strict adherence to soldering quality requirements for all assembly types |
IPC-7711/7721 | Rework, Modification, and Repair | Standardized procedures for any necessary rework operations |
ISO 9001 | Quality Management System | Comprehensive quality management across all operations |
ISO 14001 | Environmental Management System | Environmentally responsible manufacturing practices |
Our technicians are IPC-certified and regularly undergo skills verification to maintain exceptional workmanship standards across all projects. This commitment makes us a leading printed circuit board assembly electronic components’ provider in the industry.
Our PCB components assembly manufacturers capabilities extend from simple boards to the most complex electronic systems:
Industry | Application Examples | Special Requirements Addressed |
---|---|---|
Consumer Electronics | Smart devices, Audio equipment, Home appliances | High-volume capacity, Cost-effective solutions |
Industrial Controls | PLC systems, Motor controls, Sensor assemblies | Extended temperature ratings, Vibration resistance |
Medical Devices | Patient monitoring, Diagnostic equipment, Implantable electronics | Class 3 quality standards, Enhanced cleanliness |
Automotive | Engine control units, Infotainment systems, Safety components | Temperature cycling resistance, Conformal coating |
From prototypes to production, our scalable PCB fabrication and assembly capabilities accommodate virtually any electronic product requirement. Whether you need a simple PCB board or a complex two-sided PCB with a variety of components, we deliver superior results.
Mon-Fri: 24 hours,
Sat: 9am-6pm, GMT+8
Reach us at
[email protected]
24 hours online
+86-199-30589219
Mon-Fri: 24 hours,
Sat: 9am-6pm, GMT+8
Copper PCB vs. aluminum PCB comparison shows copper provides approximately twice the thermal conductivity (380-400 W/mK vs. 150-220 W/mK). While aluminum and copper are both effective for thermal management, copper substrate PCB options deliver superior performance for the most demanding applications where aluminum oxide and silicon powder dielectrics aren’t sufficient.
Yes, OurPCB offers advanced PCB solutions including 8-layer copper core PCB designs. Our copper base PCBs support complex multilayer structures with various PCB materials and copper layers to meet your specific requirements. We excel in PCB fabrication and assembly for projects requiring these specialized capabilities.
Our copper core PCB suppliers conduct comprehensive thermal validation using infrared thermography. This testing verifies actual heat dissipation across the entire board surface and identifies potential hot spots. Our PCB factory also performs reliability testing to ensure consistent performance under various operating conditions.
Prototype cable assemblies are the very important place in between PCB design ideas and interconnects. OurPCB brings prototype assemblies with PCB solutions to your tables.
PCB thermal management prevents component overheating through strategic heat transfer techniques. Without proper thermal control, electronics are at risk of electronic failures through weakened solder
ContentsKey TakeawaysWhat is a Multilayer-Printed Circuit Board?How do Multilayer PCB Boards Work?Multilayer PCB ApplicationsMultilayer PCB Manufacturing Process: StepsMultilayer PCB Manufacturing MachinesBenefits of Multilayer Circuit BoardsWhat
As electronics continue to miniaturize while processing power increases, the resulting thermal challenges make high-Tg PCBs increasingly essential for modern electronic design. ContentsKey TakeawaysWhat is
Running a computer system requires computer memory. In the entire computer system, it’s one of the vital components. Therefore, it’s important that you have basic
Electronic enthusiasts developing a circuit project may want to think about whether or not they should integrate an FFC vs. FPC. Both cables possess varying
We use cookies to improve your browsing experience, which may include personal information. By clicking "Agree," you accept our Privacy Policy and cookie use. You can change your cookie settings in your browser anytime.
Agree