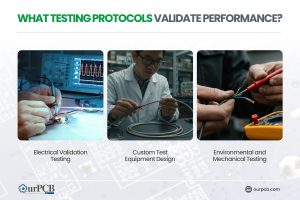
Prototype Cable Assemblies
Prototype cable assemblies are the very important place in between PCB design ideas and interconnects. OurPCB brings prototype assemblies with PCB solutions to your tables.
Looking for a top-tier manufacturer for Flexible PCBs or Rigid-Flex PCBs? OurPCB delivers high-quality, custom-designed solutions with industry-leading specifications.
Below is a detailed overview of our Flex & Rigid-Flex PCB capabilities, showcasing the key specifications and performance metrics that highlight our commitment to precision and quality in every project.
Project Item | Normal Capability |
---|---|
FPC Base Material (Adhesive) | ShengyiSF302:PI=0.5 mil,1 mil,2 mil;Cu=0.5 oz,1 oz ShengyiSF305:PI=0.5 mil,1 mil,2 mil;Cu=0.33 oz,0.5 oz,1 oz |
FPC Base Material (Adhesiveless) | SongxiaRF-775/777:PI=1 mil,2 mil,3 mil;Cu=0.5 oz, 1 oz (Ultimate:PI=1 mil,2 mil,3 mil;Cu=2 oz) Xinyang:PI=1 mil, 2 mil;Cu=0.33 oz, 0.5 oz, 1 oz Taihong PI=1 mil, 2 mil;Cu=0.33 oz, 0.5 oz, 1 oz Dubang AP:PI=1 mil, 2 mil, 3 mil, 4 mil;Cu=0.5 oz, 1 oz (Ultimate:PI=1 mil,2 mil,3 mil,4 mil;Cu=2 oz) |
Layer | 1-6 Layers (Ultimate:7-10 Layers) |
Thickness of Finished Product (Flex part,no stiffener) | 0.05-0.5 mm (Ultimate: 0.5- 0.8 mm) |
Size of Finished Products(Min) | 5 mm*10 mm (Bridgeless);10 mm*10 mm (Bridge) Ultimate:4 mm*8 mm (Bridgeless);8 mm*8 mm (Bridge) |
Size of Finished Products (Max) | 9 inch*14 inch Ultimate:9 inch*23 inch (PI≥1 mil) |
Impedance Tolerance | Single-Ended:±5Ω(≤50Ω),±10%(>50Ω) Ultimate:Single-Ended:±3Ω(≤50Ω),±8%(>50Ω) |
Impedance Tolerance | Differencial:±5Ω(≤50Ω),±10%(>50Ω) Ultimate:Differencial:±4Ω(≤50Ω),±8%(>50Ω) |
Tolerance of Finger Width | ±0.1 mm (Ultimate:±0.05 mm) |
Min Distance to the Edge of Finger | 8 mil (Ultimate:6 mil) |
Min Distance between Pads | 4 mil (Ultimate:3 mil) |
Minimum Laser Hole | 0.1mm |
Minimum PTH | 0.3mm |
Min NPTH Tolerance | ±2 mil (Ultimate +0,-2 mil or +2 mil,-0) |
Solder Bridge Min Width(bottom copper<2OZ) | 4 mil(Green),8 mil |
Solder Bridge Min Width(bottom copper 2-4OZ) | 6 mil,8 mil |
Overlay Colour | White、Yellow (printed character:White) |
Type of Surface Treatment | OSP HASL, Lead free HASL, Immersion gold, Hard gold, Immersion silver, OSP |
Selective Surface Treatment | ENIG+OSP,ENIG+G/F |
Project Item | Normal Capability |
---|---|
FPC Base Material (Adhesive) | Shengyi SF302, Shengyi SF305 |
FPC Base Material(Adhesiveless) | Songxia RF-775/777, Xinyang, Dubang AP |
Low flow prepreg | Taiguang EM-37B; Ventec: VT-47N |
Common rigid board material | Refer to standard rigid board materials |
Special rigid board material | Arlon: 85N; Rogers: RO4000 series; Nelco: N4000-13 series; Ventec: VT-901 |
Layer | 2-30 Layers; review required: ≥20 layers |
Thickness of Finished Product | 0.3-4.0mm; review required: >3.0 mm |
Size of Finished Products(Min) | 10mm*15mm (no internal positioning designs, panel size <50mm*50mm) |
Size of Finished Products (Max) | 18inch*22inch; Ultimate:18inch*29inch |
On average, flexible PCBs can range from $0.50 to $5.00 per square inch for standard designs and materials. However, this cost is not fixed and can vary based on several factors. The factors that influence the price include necessary assembly labor, prevailing labor rates, and the time required for assembly. Additionally, overhead manufacturing expenses and the design complexity of the board play significant roles in determining the final cost. To get a more accurate cost estimate, please use our free pcb quote form.
Service Type | Lead Time |
---|---|
Standard PCB Manufacturing | 5-6 days |
Expedited Manufacturing | 24-48 hours |
PCB Prototyping (Quick Turn) | 1-12 layers: within 72 hours |
12+ layers: within 120 hours | |
PCB Assembly | 4-25 days, depending on complexity and order volume |
Service Type | Lead Time |
---|---|
Standard PCB Manufacturing | 5-6 days |
Expedited Manufacturing | 24-48 hours |
PCB Prototyping (Quick Turn) | 1-12 layers: within 72 hours |
12+ layers: within 120 hours | |
PCB Assembly | 4-25 days, depending on complexity and order volume |
Step 12: Singulation and packaging
OurPCB offers flexible PCBs for innovative, space-saving designs. Starting at $172.50 for 5 units (1 layer, 100 mm x 100 mm), these PCBs are ideal for applications requiring flexibility and precision.
Mon-Fri: 24 hours,
Sat: 9am-6pm, GMT+8
Reach us at
[email protected]
24 hours online
+86-199-30589219
Mon-Fri: 24 hours,
Sat: 9am-6pm, GMT+8
Flexible PCBs can be bent, shaped, wrapped, or folded into any 2D or 3D shape. These features make flexible PCBs perfect for use in medical and surgical equipment, consumer electronics, automotive and space applications, and smart wearable devices.
We have no minimum order quantity, allowing you to order anything from single prototypes to mass production runs.
Prototype cable assemblies are the very important place in between PCB design ideas and interconnects. OurPCB brings prototype assemblies with PCB solutions to your tables.
PCB thermal management prevents component overheating through strategic heat transfer techniques. Without proper thermal control, electronics are at risk of electronic failures through weakened solder
ContentsKey TakeawaysWhat is a Multilayer-Printed Circuit Board?How do Multilayer PCB Boards Work?Multilayer PCB ApplicationsMultilayer PCB Manufacturing Process: StepsMultilayer PCB Manufacturing MachinesBenefits of Multilayer Circuit BoardsWhat
As electronics continue to miniaturize while processing power increases, the resulting thermal challenges make high-Tg PCBs increasingly essential for modern electronic design. ContentsKey TakeawaysWhat is
Running a computer system requires computer memory. In the entire computer system, it’s one of the vital components. Therefore, it’s important that you have basic
Electronic enthusiasts developing a circuit project may want to think about whether or not they should integrate an FFC vs. FPC. Both cables possess varying
We use cookies to improve your browsing experience, which may include personal information. By clicking "Agree," you accept our Privacy Policy and cookie use. You can change your cookie settings in your browser anytime.
Agree