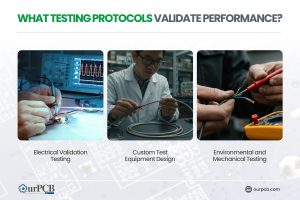
Prototype Cable Assemblies
Prototype cable assemblies are the very important place in between PCB design ideas and interconnects. OurPCB brings prototype assemblies with PCB solutions to your tables.
✅ Custom Prototyping: Rapid turnaround for custom plastic prototypes.
✅ Cost-Effective Production: Economical for high-volume production of identical plastic parts.
✅ Material Variety: Supports diverse materials, including thermoplastics and elastomers.
✅ Quality Assurance: Offers inspection and certification for compliance with industry standards.
✅ Diverse Applications: Serves multiple industries, including medical, automotive, and consumer products.
Are you searching for a world-class injection molding service provider? OurPCB specializes in delivering high-precision injection molding with a focus on quality, efficiency, and customer satisfaction. As a premier injection molding partner trusted by industry leaders across the United States, we deliver precision-engineered solutions that drive innovation and cost-effectiveness in American manufacturing.
With a focus on client satisfaction, premium products, and competitive pricing, we are committed to meeting all your injection molding needs. Contact us today for an accurate quote or consultation—we look forward to working with you on your next project.
The cost of injection molding services typically depends on several key factors: the complexity and size of the part, the material used, the production volume, and the mold (tool) cost. Mold costs can range from $1,000 for simple designs to over $100,000 for complex, multi-cavity molds. Material costs vary widely, from $1-$3 per pound for common plastics to $30+ per pound for specialized engineering plastics. Machine time and labor also contribute to the overall cost.
For high-volume production, the per-unit cost decreases significantly as the mold cost is spread over more parts. While initial tooling costs can be high, injection molding becomes more cost-effective for large production runs, often resulting in lower per-unit costs compared to other manufacturing methods.
Note* For exact prices, contact OurPCB directly. Our team will look at your project needs and give you a clear quote. Costs change based on what you need and current market prices. We offer fair pricing for all injection molding projects. Get in touch with us today to discuss your needs.
Let’s break down the process step by step for a comprehensive understanding.
The first step in injection molding involves preparing the raw material:
Once the material is loaded, it needs to be melted:
After the plastic is fully melted, it’s ready for injection:
Once the mold is filled, there’s a brief pause called the dwelling phase:
The cooling phase is crucial for part quality:
After the part has cooled sufficiently:
The final step prepares the machine for the next cycle:
Rapid Mold Process: We employ CNC rough machining, EDM (electrical discharge machining), mold fitting, mold debugging, mold assembly, mold installation, and injection molding to produce the mold and product swiftly.
Next, the process involves removing injection molding residuals, retrieving the finished products, and trimming residuals. We’ll finish off the process with a manual quality inspection as well as a 3D inspection. The mold and product can be completed in 10 days.
Processing Accuracy: ±0.1 mm/100 mm
Injection Molding Tonnage: 80 to 3000 tons
Only ROHS-compliant materials
Orange or OEM color
TUV, ISO9001, T/S16949, ROHS-approved
Prototypes can be provided for assessment
Small quantities accepted
100% TT or PayPal for convenience
As fast as possible based on production capacity
✔️ PET (Transparent) | ✔️ PPSU |
✔️ POM | ✔️ SAN |
✔️ PC (Transparent, Opaque, Medical Grade, Flame Retardant) | ✔️ ABS (Transparent, Flame Retardant) |
✔️ PC+GF | ✔️ ABS+UV resistant |
✔️ PBT | ✔️ ABS+GF |
✔️ PBT+GF | ✔️ PC+ABS (Standard, Medical Grade, Flame Retardant, High Gloss) |
✔️ PA6 | ✔️ PP (transparent, opaque) |
✔️ PA6+GF | ✔️ PP+GF |
✔️ PA66 | ✔️ PE (Transparent, Opaque, +PE Modified) |
✔️ PA66+GF | ✔️ GPPS (Transparent) |
✔️ PPA | ✔️ HIPS (Natural Color, Modified) |
✔️ PPA+GF | ✔️ ABA (Transparent) |
✔️ PPS | ✔️ TPU (Transparent, Opaque, Various Hardness) |
✔️ PMMA | ✔️ TPE (Transparent, Opaque, Various Hardness) |
As your top injection molding service supplier, our skilled staff provides timely online injection molding quote and real-time order status tracking.
We combine numerous processes to provide one-stop prototype and product processing services, including advanced CNC machining, 3D printing, silicone molding, rapid and injection molding, sheet metal processing, and multiple surface treatment technologies.
We are ISO 9001, ISO 14001, IATF 16949, and ISO 27001 certified, and we have a well-established quality control system.
With superior client satisfaction, high-quality goods, and affordable rates, we aspire to be the best choice for all of your injection molding service requirements.
Contact us today to receive an accurate quote or consultation. We look forward to working with you on your next project.
Mon-Fri: 24 hours,
Sat: 9am-6pm, GMT+8
Reach us at
[email protected]
24 hours online
+86-199-30589219
Mon-Fri: 24 hours,
Sat: 9am-6pm, GMT+8
Injection molding is a manufacturing process that mass-produces thousands of identical plastic components. It involves injecting the molten material (usually thermoplastic and thermosetting polymers) into a mold fitted into the machine.
These molds are precision-machined to match the shape of the final product. They also have cooling lines that reduce the solidification time by circulating water or oil from an external temperature controller after material injection.
Besides plastics, the process can make metal (die-casting), glass, confections, and elastomer parts, which can also be utilized by PCB manufacturing companies for creating various electronic components.
Prototype cable assemblies are the very important place in between PCB design ideas and interconnects. OurPCB brings prototype assemblies with PCB solutions to your tables.
PCB thermal management prevents component overheating through strategic heat transfer techniques. Without proper thermal control, electronics are at risk of electronic failures through weakened solder
ContentsKey TakeawaysWhat is a Multilayer-Printed Circuit Board?How do Multilayer PCB Boards Work?Multilayer PCB ApplicationsMultilayer PCB Manufacturing Process: StepsMultilayer PCB Manufacturing MachinesBenefits of Multilayer Circuit BoardsWhat
As electronics continue to miniaturize while processing power increases, the resulting thermal challenges make high-Tg PCBs increasingly essential for modern electronic design. ContentsKey TakeawaysWhat is
Running a computer system requires computer memory. In the entire computer system, it’s one of the vital components. Therefore, it’s important that you have basic
Electronic enthusiasts developing a circuit project may want to think about whether or not they should integrate an FFC vs. FPC. Both cables possess varying
We use cookies to improve your browsing experience, which may include personal information. By clicking "Agree," you accept our Privacy Policy and cookie use. You can change your cookie settings in your browser anytime.
Agree