Every day, PID (proportional integral derivative) controllers are widely used in industrial control applications to regulate temperature, pressure, flow, speed, pressure, and other process variables. These instruments control process variables using a control loop feedback mechanism. They’re the most stable and accurate controllers.
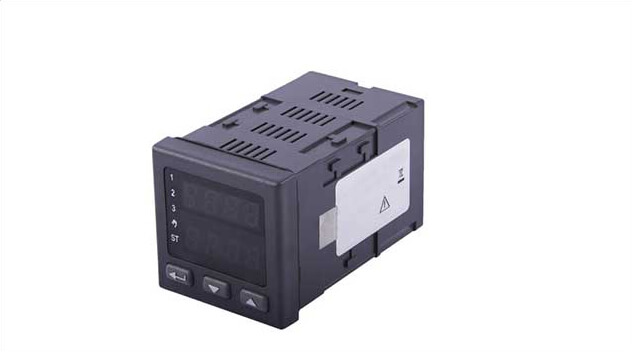
As we mentioned earlier, a PID controller can effectively control temperature, flow, pressure, and such process variables. The instrument combines proportional control with other integral and derivative adjustments that assist the unit to make up for any changes in the system automatically.
1.1 The Basics of a PID Controller
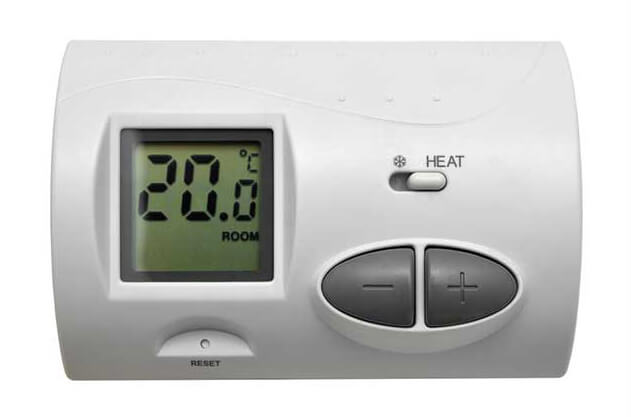
1.2 The Working Principle PID Controllers
The main working principle behind a PID controller entails the individual adjusting or tuning of the proportional, integral, and derivative terms. A correction factor calculates and applied to the input based on the differences between the three values. Here’s an example: when your oven is more relaxed than your desired level, the heat will increase.
Let’s look at the three steps:
Step 1: Proportional Tuning
In proportional tuning, the target comparable to the difference correct. The target value never achieves since, as the difference moves towards zero, the applied correction does the same.
Step 2: Integral Tuning
The purpose of integral tuning is to attempt to remedy the situation in proportional adjustment by cumulating the error result from the “P” action to add the correction factor. Here’s a good example: if in equivalent tuning, the oven stayed below temperature, the necessary adjustment would increase the amount of heat delivered. However, “I” action does not stop once the target reached. Instead, it tries to drive the cumulative error to zero. The result is an overshoot.
Step 3: Derivative Tuning
In this final step, derivative tuning tries to minimize the overshoot from the “I” action. It does so by slowing the correction factor that’s applied as the target approached.
2、How to Adjust the PID Value
PID control may appear simple in concept, but the mathematics behind the process is rather complicated. For the best performance, process-specific values for a wide range of interacting parameters need to be selected. The method of selecting these values referred to as tuning.
Once appropriately tuned, a PID temperature controller will keep deviations from the desired set point to a minimum and quickly respond to any disturbances to the set point. In this section, we’ll discuss several methods of tuning a PID temperature controller.
2.1 PID Controller Tuning Methods
Before we discuss the proper ways of tuning a PID temperature controller, it’s important to note that every process has its unique characteristics, even when the equipment is similar. Why? Because the airflow around ovens varies, barometric pressure changes from hour to hour, and ambient temperatures can alter the density and viscosity of a fluid.
That said, let’s look at the three broad approaches to tuning PID temperature controllers.
2.1.1 Zeigler-Nichols (ZN) Method
First released in 1942 Ziegler-Nichols method This method describes two approaches to adjusting a PID loop. In the first method, the lag or delay in response is measured, in addition to the time taken to reach the final output value. The second approach entails establishing the period of a steady oscillation. Each method’s measured values are entered in a table to give gain, reset time, and rate benefits.
The Ziegler-Nichols method has its issues. For instance, the technique produces a response that’s too aggressive when it comes to oscillation and overshoot. Secondly, when applied to processes that react slowly, the procedure can be time-consuming.
2.1.2 Manual Tuning
In manual tuning, you set the reset time to its optimum value. You then set the rate is zero. Increase the gain until the loop oscillates at a consistent amplitude. Then increase the speed until the level of overshoot minimizes. After this, a fixed benefit to half of the value and adjust the rest time to rectify any offset within a reasonable period.
2.1.3 Auto Tuning
The vast majority of PID process controllers come with auto-tuning functions. The PID controller learns how the process reacts to changes or disturbances in the desired set point. The controller then automatically calculates the appropriate PID settings. The latest controllers have fuzzy logic and automatic adjustments. Can handle nonlinearities and inaccuracies in complex control situations. Such situations are regularly encountered in the process and manufacturing industries.
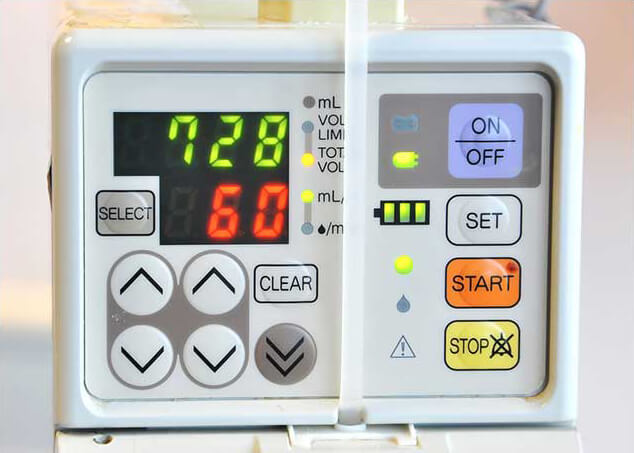
Special Offer: Get $100 off your order!
Email [email protected] to get started!
3、Programming the Controller, You Can Use the Software
The process of tuning a PID temperature controller seems simple at first. One only needs to set three gain values: the proportional, integral, and derivative gains. In reality, however, the process of systematically and safely achieving the perfect set of these gain values can be rather complicated. PID tuning software aims to simplify this process. There’s, of course, a wide variety of software in the market that can help in PID controller tuning. We’ll look at two of the most popular PID controller software.
3.1 Simulink Software
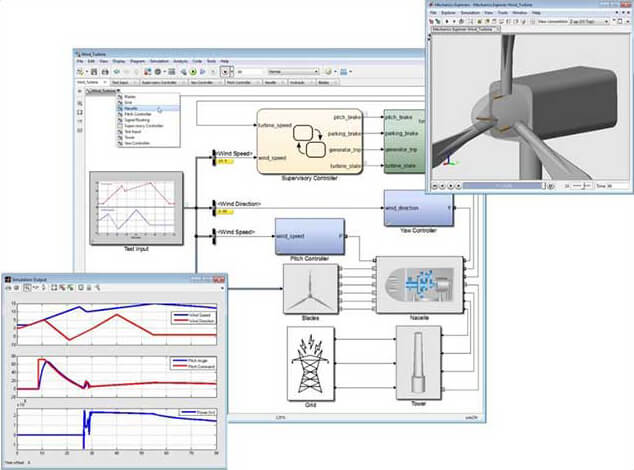
3.2 LOOP-PRO
4、Things You Need To Be Aware Of
Once you have successfully installed your PID temperature controller, one of the most important things you’ll need to pay attention to is how to maintain the device properly. Taking care of the controller can significantly extend its useful life. Below are a few maintenance tips you can apply for your PID temperature controller:
- Regularly remove the grain deposited at the bottom of the air supply tube. To do this, loosen the drain plug at the bottom of the filter regulator.
- Be careful always to maintain the air pressure at 140kPa.
- When you notice that the air filter’s performance is no longer stable, consider repairing or replacing it.
- Inspect the orifice holes of the nozzle or pilot relay based on the conditions of the air supply
- Every once in a while, press the orifice cleaning button to clean the orifice.
- Whenever necessary, disassemble and unclog the nozzle.
These basic maintenance practices can go a long way in keeping your PID controller functioning optimally for a long time.
5、Fields in the PID Temperature Controller
PID temperature controllers use in over 99% of all loops needed for food, chemical, and pharmaceutical production. Below are some specific applications where these controllers are applied:
- Heat treatment of metals. In this application, PID controllers ensure precise control of ramp and soak processes, hence achieving the desired metallurgical properties.
- Drying and evaporating solvents from painted surfaces. Excessive temperatures can cause damage to substrates, while too low temperatures can result in the reduced appearance of products or even product loss.
- Curing rubber. For complete curing of rubber without adverse effects on the material properties, there’s a need for precise temperature control.
- Baking. All commercial ovens must stick to strictly prescribed heating and cooling sequences. This helps ensure that all necessary reactions take place.
- Motion control. All motion control systems utilize some form of PID control. These systems, however, require some particular kind of controller because the response is faster in these systems.
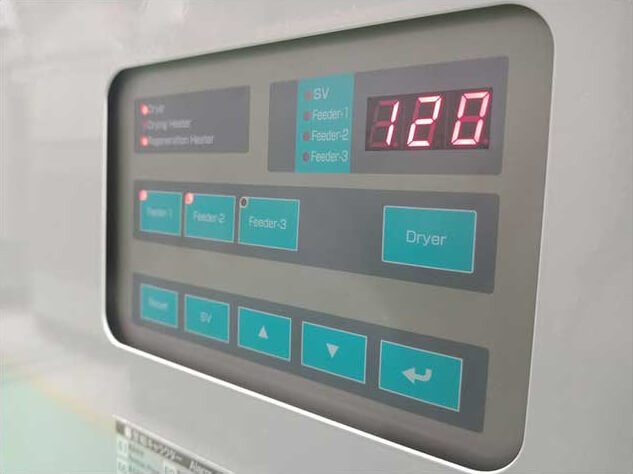
6、Summary
Each year, millions of PID temperature controllers are used to control industrial processes worldwide. In almost all heat processes, PID temperature control is necessary to ensure consistent product quality. That’s because the temperature inside the furnace or oven needs to be kept within strictly narrow limits. Any disturbance, for instance, when there’s an addition or withdrawal of a product or the application of a ramp function, must be appropriately handled. This is the job of the PID temperature controller.
Would you like PID temperature control solutions that suit your needs? At WellPCB, We have just what you need. Please get in touch with us or visit our website today to learn more.
Special Offer: Get $100 off your order!
Email [email protected] to get started!