Contents
Special Offer: Get $100 off your order!
Email [email protected] to get started!
What is the meaning of PCB OSP Plating Surface Finish?
OSP (Organic Solderability Preservative) is a surface finish applied to printed circuit boards (PCBs). It provides two key functions:
- Solderability: OSP helps ensure the solder adheres to the copper pads during assembly.
- Copper Protection: It forms a protective layer over exposed copper, preventing oxidation.
OSP is a cost-effective, lead-free, and environmentally friendly option commonly used in PCB manufacturing. However, its protective qualities degrade over time, making it ideal for boards that will be assembled within 6-12 months of production. It is most suitable for low-volume prototypes and applications requiring a flat, solderable surface.
OSP PCB Applications
OSP plating is widely used in the following applications:
- Low-Volume Prototypes: Due to its low cost, OSP is suitable for prototype runs and engineering tests before large-scale production.
- Double-Sided PCBs: It is ideal for double-sided boards, reducing the overall production cost while maintaining solderability on both sides.
- Automated Assembly: OSP’s excellent wetting properties make it compatible with automated PCB assembly lines, including pick-and-place machines and reflow soldering.
- Manual Soldering: The finish remains solderable even after 6-12 months of storage, making it ideal for hand-soldered components that aren’t assembled immediately.
Engineering Testing: OSP is often used for engineering testing before large-scale production, offering a cost-effective solution while maintaining good solderability.
Advantages | Disadvantages |
Low Cost: OSP is one of the most affordable surface finishes available. | Short Shelf Life: Typically 6-12 months before oxidation may occur. |
Environmentally Friendly: Uses water-based compounds, compliant with RoHS and other green regulations. | Poor Mechanical Durability: The thin, transparent layer is prone to scratches and damage, making visual inspection difficult. |
Lead-Free: OSP is a lead-free finish, making it compliant with RoHS and suitable for lead-free assembly. | Limited Reflow Cycles: Can only withstand 4-6 reflow cycles before degradation. |
Good Solderability: Offers excellent wetting and solderability, even after extended storage. | Moisture Sensitivity: OSP is highly sensitive to humidity and requires careful handling to avoid oxidation. |
Flat Surface: Provides a smooth surface, ideal for fine-pitch components like BGAs and QFPs. | Not Suitable for Heavy Wear: The thin coating can wear down during handling or automated assembly processes. |
Repairability: Damaged OSP coatings can be reapplied if needed. | Difficult Thickness Measurement: Due to its transparency, it is hard to measure the film's thickness, which can lead to inconsistent protection. |
Compatible with Automated Assembly: Suitable for use in automated pick-and-place processes. | Not Ideal for Multiple Reflows: Prolonged or repeated soldering cycles can wear down the OSP layer quickly. |
OSP Manufacturing Process
The OSP process involves multiple stages to ensure a smooth, reliable coating on the PCB:
- Cleaning: The copper surface is cleaned to remove contaminants such as oils, oxidation, and fingerprints.
- Topography Enhancement: Micro-etching is performed to improve the bonding between the copper and the OSP layer by removing oxidation.
- OSP Application: The water-based organic solution is applied to the copper surface, forming a protective layer.
- Deionized Water Rinse: The board is rinsed with deionized water to remove any residual ions that may affect the solderability.
- Drying: The boards are dried, preparing them for storage or further processing.
Maintaining a stable micro-etching speed, typically between 1.0 to 1.5 μm per minute, is essential to achieve a uniform film thickness, which is critical to the effectiveness of the OSP coating.
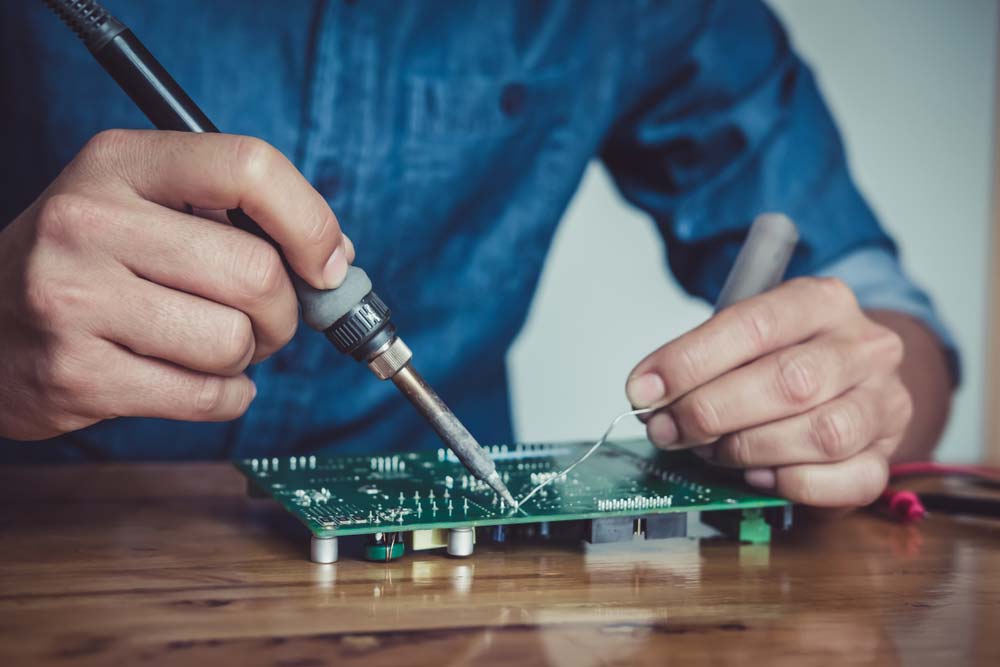
What are OSP PCB Finish Problems?
Our team at OurPCB has prepared a list of OSP PCB coating issues:
- Poor Wetting During Soldering: OSP can lead to poor wetting due to contamination, degradation of the coating, or insufficient fluxing, resulting in unreliable solder joints, especially under components like BGAs.
- Chemical Attack: OSP coating can be compromised by exposure to strong acids, bases, or aggressive cleaning agents, leading to copper corrosion and solderability issues.
- Thickness Variation: Variations in the OSP layer’s thickness can hinder soldering if too thick or fail to prevent oxidation if too thin.
- Handling and Storage Sensitivity: OSP is sensitive to high temperatures and humidity, which can degrade the film. Proper storage conditions are crucial to maintaining effectiveness.
- Oxidation Vulnerability: OSP coatings are prone to oxidation, especially in high humidity or if stored improperly.
- Difficult Inspection: The thin, transparent layer makes it hard to inspect for complete coverage.
- Limited Reflow Cycles: OSP finishes typically last for 4-6 reflow soldering cycles before degrading.
- Mechanical Fragility: OSP layers are easily damaged by handling, scratches, or moisture exposure.
- Short Shelf Life: OSP coatings have a limited shelf life of 6-12 months, reducing long-term usability.
- Reduced Solderability Over Time: As OSP degrades, it exposes copper surfaces, diminishing solderability.
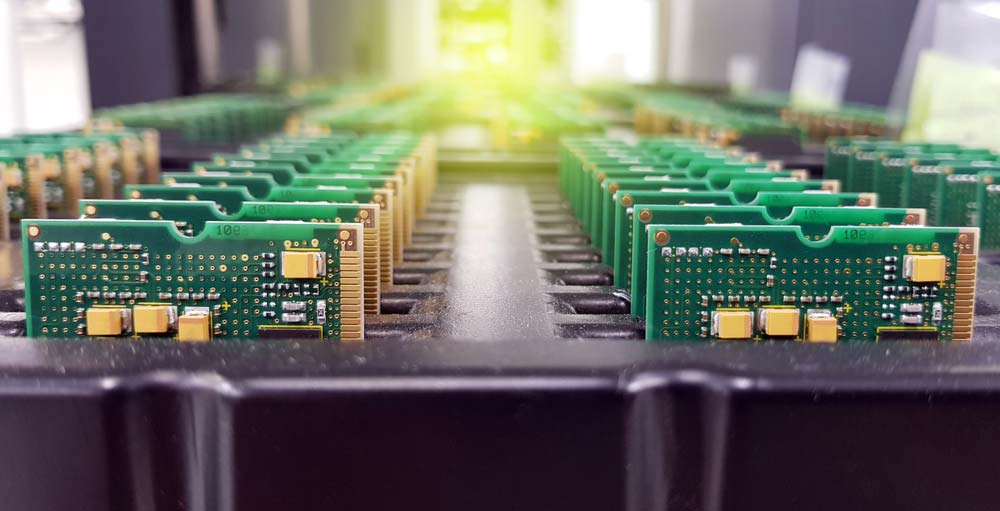
What are OSP PCB Plating Alternatives?
An alternative to OSP plating are surface finishes like ENIG (Electroless Nickel Immersion Gold) and HASL (Hot Air Solder Leveling). While ENIG offers a longer shelf life and superior protection against oxidation, it is more expensive. HASL, though relatively affordable, results in a less flat surface, making it unsuitable for high-density components.
Special Offer: Get $100 off your order!
Email [email protected] to get started!